About Us
Creating Innovative Energy Systems for a Cleaner World
TransPacific Energy’s (TPE) vision is to create innovative energy systems for a cleaner world.
The Problem and the Solution:
Problem: Of the estimated 500,000 smokestacks in the United States, 47,500 represent up to 75% of untapped waste heat at above 500 F. This waste heat could generate at least 50,000 megawatts of power. Utilizing this waste heat could generate more than $100 billion in gross revenues.
Solution: TransPacific’s custom-designed technology targets this market by capturing waste heat and efficiently converting it into power from flue gas at temperatures between 250 F to 500 F. TPE can also efficiently recover waste heat at temperatures higher than 500 F.  TransPacific Energy’s power plant retrofits create electricity that can be used in industry or sold back to the utility company at regulated rates, with a high rate of return on the initial project investment.
Problem: Previously, other markets, such as geothermal and thermal solar, required a minimum of 300ºF to cost-efficiently produce energy.
Solution: TPE’s technology permits cost-efficient recovery of waste heat at temperatures lower than 200º F . TPE’s ability to use such low temperatures means abandoned oil wells that have been capped could become viable energy-producing opportunities.
Our Unique Difference: TransPacific Energy has developed a patent on a heat recovery/energy conversion system that produces electricity from many heat sources. These include hot flue gases from the process industry, biomass, landfill, solar, geothermal, gray water/hot fluids, and warm ocean waters. The system uses custom-tailored advanced Organic Rankine Cycles (ORC) with patented, environmentally sound multiple refrigerant mixtures. This custom-tailored design maximizes power production and can easily be adapted to a broad range of heat sources and temperatures. TPE’s technology can be used where other refrigerants such as ammonia, propane, butane and other HCFCs and HFCs have limited applications.
TPE’s process directly captures and converts heat directly from the heat source, without any heat transfer fluids (Binary Cycle), at temperatures from 80ºF up to 900ºF. This is a far broader range than any other ORC systems on the market. Other ORCs are limited to temperatures of around 200ºF to 350ºF. Because of the limited temperatures, other ORCs must use a binary system or secondary heat transfer to recover waste heat at higher temperatures. Using a binary system or secondary heat transfer significantly reduces heat recovery efficiency and increases costs.
TransPacifc Energy’s technology eliminates the need for a binary heat exchange system or secondary heat transfer. This is because TPE recovers waste heat directly and at much higher efficiencies.
TPE offers you a substantial advantage:  Our patent blend of multiple refrigerants enables us to custom engineer the highest efficiencies tailored to your heat source and flow to yield greater power (from 6% to 30%). TransPacific Energy’s unique technology offers:
Enhanced heat-to-power efficiency, availability higher than 98%.
Use of air-cooled condensers, if required, instead of cooling towers to reduce cost.
Easy to install, limited footprint, low maintenance cost, simple automated operation.
Broad temperature applications.
Reduced carbon emissions and greenhouse gases and produced zero acid rain.
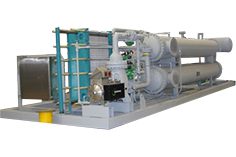
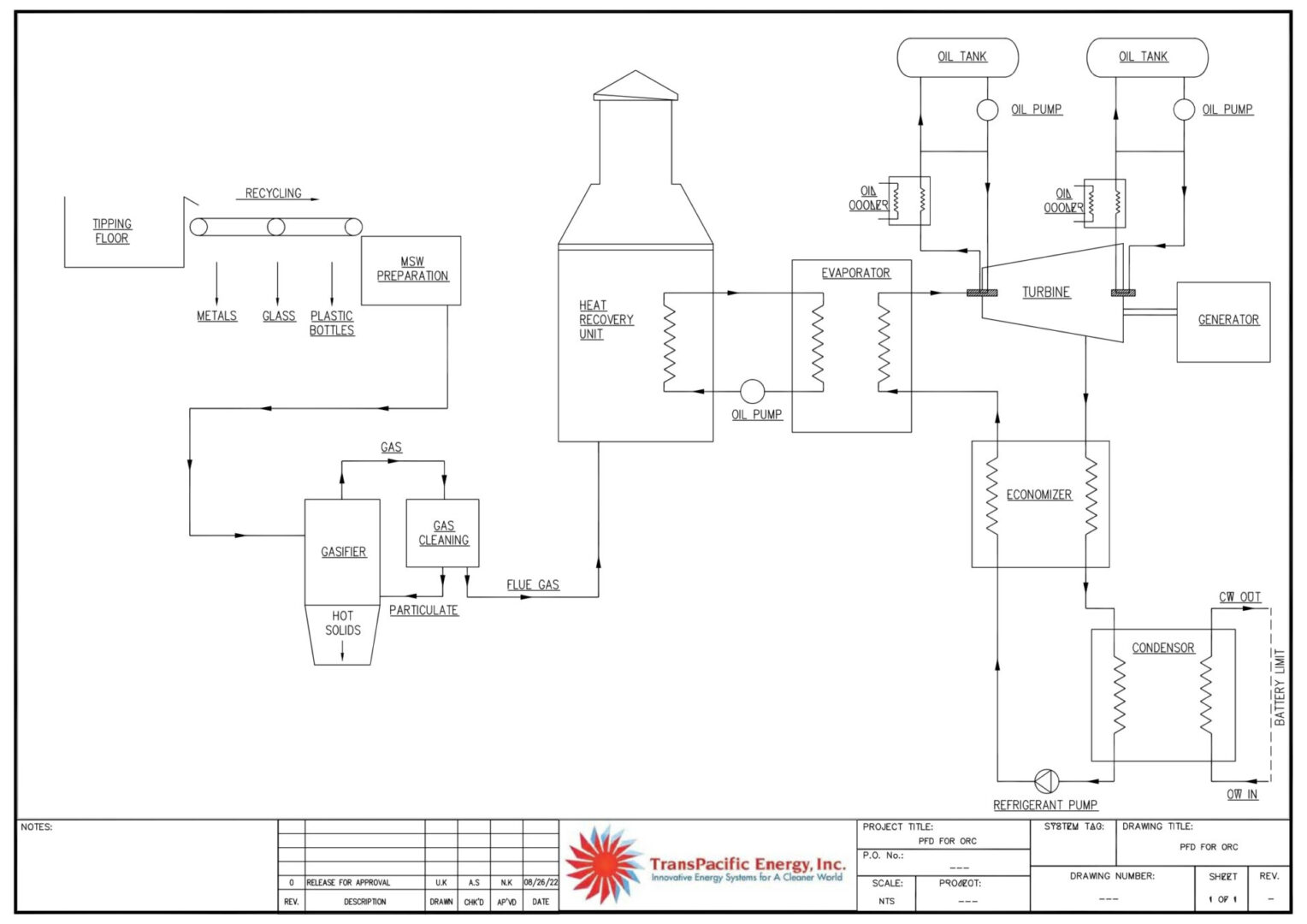
Landfill, Gasfire and ORC
Landfills are toxins, leachate, and greenhouse gases that produce bacteria that break the rubbish down. Landfills cause climate change, fires, or explosions, contaminate soil and water, and alter the fauna.
Environmental issues such as climate change and global warming, caused by the burning of fossil fuels and the huge production of waste in landfills, are bound to occur. The tremendous amount of waste generated daily in landfills has huge environmental effects. Biomass is made up of organic materials Using biomass resources for bio-hydrogen production based on feedstock can provide many benefits such as being cost-effective, environmentally friendly, and emission of no greenhouse gases such as CO2. Fermentation:
Biomass is converted into sugar-rich feedstocks that can be fermented to produce hydrogen. Biomass gasification is a well-known technology that uses a controlled process involving heat, steam, and oxygen to convert biomass to hydrogen and other products, without combustion.
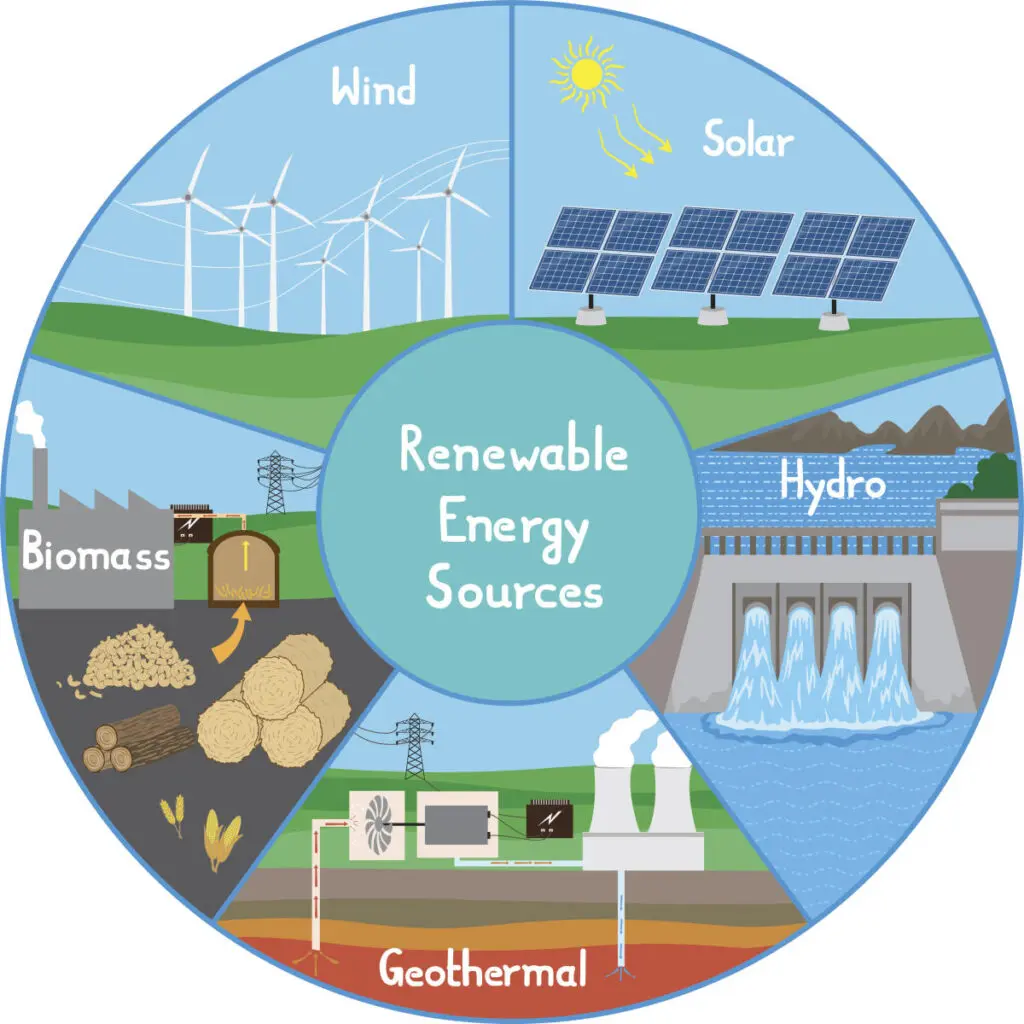
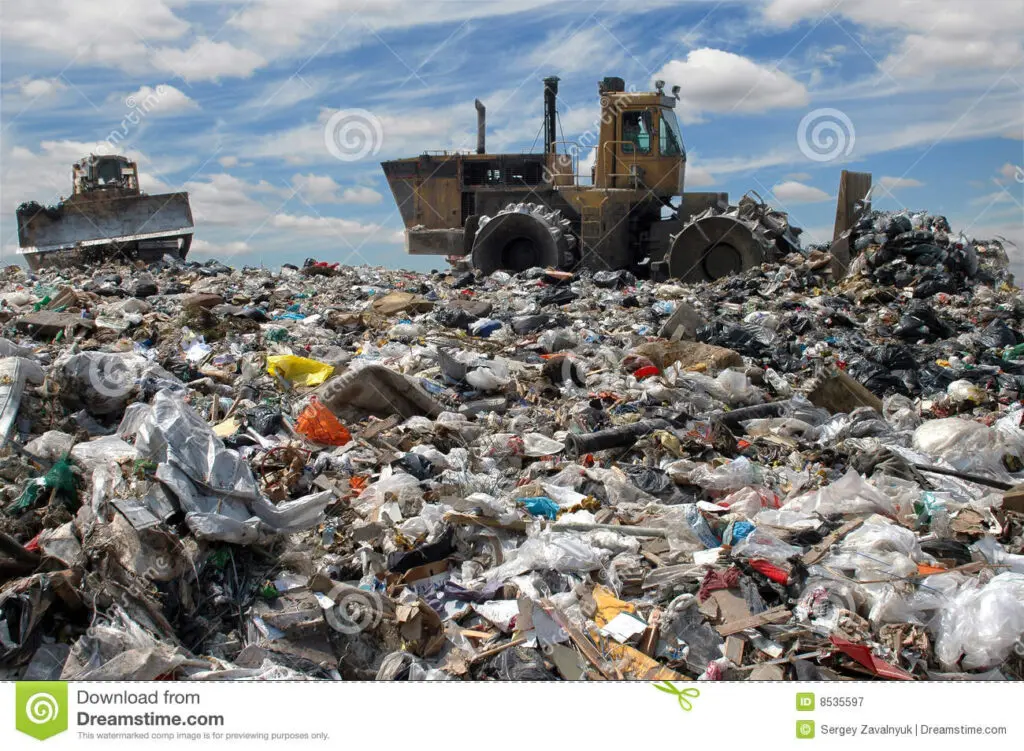
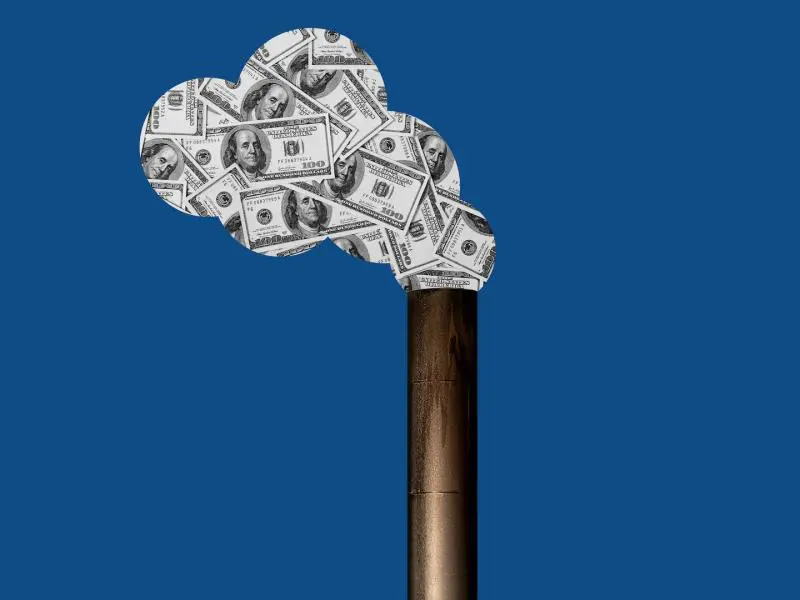
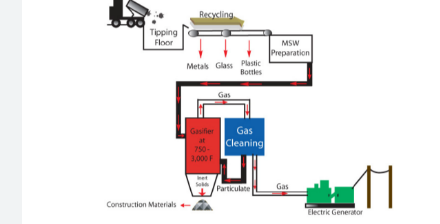
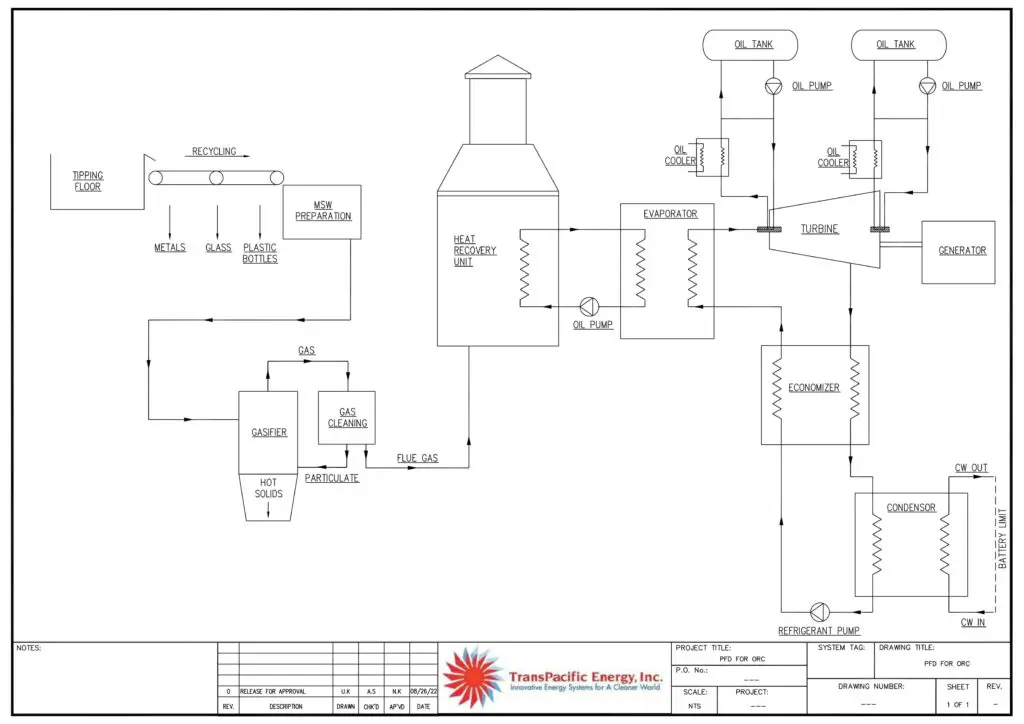
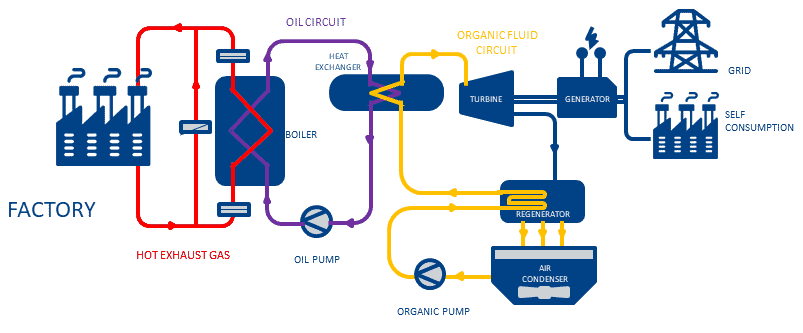
Organic Rankine Cycle Systems Comparison*
Evaporator Temperature Range (F)1 | 80-900 | 212+ | 200-210 | 200-250 | 100-150 | 200-250 | 210 | 200-250 |
Conversion Efficiency (%) 2 | 6- 30% | 11.0% | 9.3% | 10.9% | 6.7% | 8.0% | 12.6% | 14.0% |
Typical Recovery Temperature Range (F) | 80-900 | 212+ | 200-210 | 200-300 | 100-150 | 200-250 | 200-210 | 200-250 |
Gas Recovery | Yes3 | Yes | No | No | No | No | No | No |
Liquid Recovery | Yes | Yes | Yes | Yes | Yes | Yes | Yes | Yes |
Flammability | No | No | No | No | No | No | Yes4 | Explosive |
Variable Boiling Points5 | Yes | No | No | No | No | No | No | No |
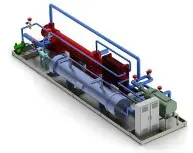
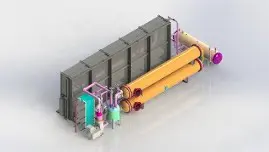
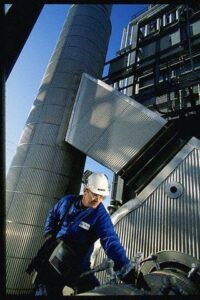
- Based on typical and recommended operating points
- Condensing 100F
- Composition can be changed to recover higher waste temperatures
- Toxic
- To recover heat at temperatures >250 F
* Typical (conditions may vary depending on manufacturer and application)
****APPLICATIONS REFERENCES:
References of Applications and Installations for ORC and ORC Integrated Systems as well as Renewable Energy Systems are available upon demand. Please contact us: 619 272 9131 or by email: information@transpacenergy .com
TransPacific Flue Gas Heat Recovery Flow Diagram
TransPacific Hot Liquid Heat Recovery Flow Diagram
TransPacific Cogeneration Heat Recovery Flow Diagram
TransPacific ICE Heat Recovery Systems Flow Diagram
Substantial Advantage TPE ORCs
TransPacific Advantage Case Studies
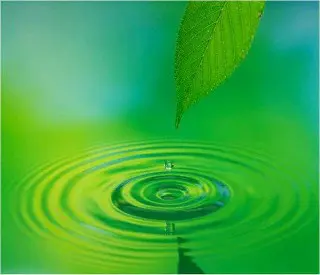
Environmental Benefits:
Zero Fuel Consumption
Environmentally Friendly/Refrigerants
Zero Pollutants Such As Carbon Monoxide, Nitrogen Oxides, and Sulfur Oxides
Zero C02 discharges KWH generated
Zero Acid Rain